Multi-Legged Hydraulic Robots
Development and Control of Multi-Legged Robots for Rough Terrain Locomotion
Since 2012, our laboratory has been applying whole-body motion control technologies developed for hydraulic humanoid robots to multi-legged robots and rovers. The goal is to realize a "mobile base" capable of traversing rough terrain with agility. By equipping this base with manipulators or other existing power tools, it can support a variety of labor-intensive tasks such as dismantling and assembling structures, transporting and removing materials and debris, and more. We consider the following features to be crucial for achieving this goal:
(A) Maintenance of the base position and orientation on uneven and/or inclined terrain
(B) Adaptation to uneven surfaces and steep slopes
(C) Impact resistance and flexibility
Here, (A) ensures the workspace for tools and manipulators remains unaffected by the terrain. (B) considers kinematic and dynamic adaptability to extreme uneven surfaces and steep slopes. (C) anticipates absorbing shocks from sudden changes in terrain (suspension functionality). This research introduces "whole-body motion control technology using joint torque control," enabling flexible responses to change in terrain shape and disturbances without relying on specialized external sensors. By coordinating the base, legs, and wheels, the system adapts seamlessly to various conditions. This represents a novel application of hydraulics, distinct from traditional approaches.
Hydraulic Quadruped Robot
In this multi-legged project, we first developed the torque-controlled hydraulic quadruped robot RL-A1 (height: 1.1 m, weight: 75 kg), based on the leg designs created during humanoid research. This robot has two versions: with or without an onboard hydraulic power unit. Each leg features three active joints (Roll–Pitch–Pitch) and optionally the passive prismatic joint at the foot tip, resulting in a total of 12 or 16 degrees of freedom for the entire robot.
Thanks to the implementation of the passive-based control framework, the robot demonstrates excellent balance capabilities on unstable terrain and can continue walking even when subjected to significant external disturbances without falling over.
HSL-A1(first appeared at IREX2013)
HSL-A1 with on-bord HPU (RSJ2016)
HYDROVER (hydraulic legs and wheels)
This is the hydraulic rover developed in collaboration with a company as part of fundamental research on agricultural mobile robots. A leg-wheel robot combines the advantages of wheels and legs. The advantages of legs include discrete contact point selection and versatile movement postures. On the other hand, the advantages of wheels are high efficiency and high-speed mobility.
This robot is capable of torque control for all its joints, including its drive wheels. Leg-wheel robots are highly compatible with whole-body motion control using force control, enabling precise manipulation of ground contact force and traction. Leveraging this feature, the robot can adjust its force to prevent uncontrollable slipping during operation. The second prototype developed under the project features three degrees of freedom per leg and one drive wheel, for a total of 16 degrees of freedom. The robot weighs 331 kg. The leg mechanisms use cost-effective proportional valves, while the drive wheels utilize servo proportional valves. By measuring the internal cylinder pressure with pressure sensors, torque control for all joints is achieved.
Hydrover I (2015)
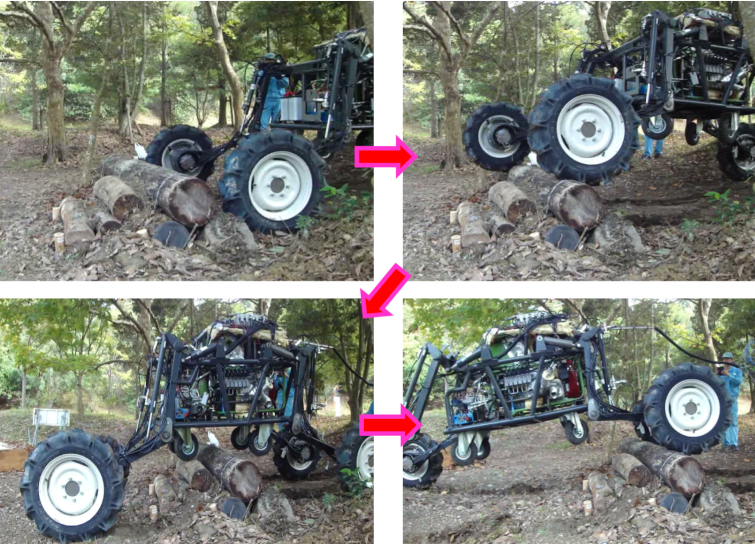
油圧ローバーによるログの乗り越えの様子(学内のフィールド実験場)
Hydrover II(2017)
CRAWHEL (hydraulic leg x 4 + electric wheels x 2 )
We are developing the robot with a "separated leg-wheel mechanism" design to assist in construction tasks on unstable terrain. This structure features legs and wheels attached separately to the main body, with the legs extending outward to create a wide support area. This configuration enhances stability by maintaining the base's position and posture. While this design is well known, combining it with our whole-body motion control technology creates new value.
Specifically, the lightweight leg mechanism incorporates hydraulic force control, allowing the robot to quickly adjust its footing and prevent tipping over even if the ground collapses suddenly (as shown in Figure d). Meanwhile, the wheels located directly under the robot's center of gravity bear most of the body weight, reducing the burden on the legs. These wheels enable high-speed movement on flat surfaces. They also play a role in vibration damping and fall prevention while maintaining ground contact. Additionally, the wheels can work in coordination with the legs to navigate large obstacles and climb high steps.
The prototype, our first model, has 16 degrees of freedom (4 legs and 2 wheels), measures 2 meters in length, and weighs 145 kg. To support outdoor operations, it is equipped with a mobile hydraulic power unit.
CRAWHEL(2015-)
Publications
- 織田健吾,松井俊樹,小野颯之介,玄相昊,“脚車輪型ロボットの冗長自由度を使ったモデル予測制御,”第28 回ロボティクスシンポジア, pp 52-55, 2023.
- 織田健吾, 井田裕介, 石川淳一, 平岡実, 玄相昊,“全身トルク制御可能な油圧ローバーの実現”,日本ロボット学会誌, vol. 40, no. 5, 2022.
- 織田健吾,松井俊樹,小野颯之介,玄相昊,“脚車輪型プラットフォームCRAWHELによる接触力と車輪接触点速度を同時決定可能な軌道追従制御,” 第23回計測自動制御学会システムインテグレーション部門講演会,pp 548-551, 2022.
- S. Hyon, Y. Ida, K. Ueda, J. Ishikawa, and M. Hiraoka, “Development of HYDROVER , a Torque-Controlled Hydraulic Rover,” Field and Service Robotics, Springer, 2021. (DOI: 10.1007/978-981-15-9460-1).
- K. Oda, Y. Yasui, Y. Kurose and S. Hyon, "Enhancement of a Leg-Wheel Mechanism by Hydraulics toward Compliantly Balancing Platforms for Heavy Duty Work,'' Advanced Robotics, Vol. 35, No. 23, PP. 1450-1467, 2021 DOI:10.1080/01691864.2021.1980102
- 織田健吾, 安井雄哉, 黒瀬裕一郎, and 玄相昊, “不整地作業用脚車輪型プラットフォームCRAWHELの開発,” in 第39回日本ロボット学会学術講演会, 2021.
- S. Hyon, Y. Ida, J. Ishikawa, and M. Hiraoka, “Whole-Body Locomotion and Posture Control on a Torque-Controlled Hydraulic Rover,” IEEE Robot. Autom. Lett., vol. 4, no. 4, pp. 4587–4594, 2019.
- 玄相昊, “油圧による柔軟で機動性の高い多脚ロボットの実現,” 日本ロボット学会誌, vol. 37, no. 2, pp. 150–155, 2019.
- 榊原康平, 井田裕介, 石川淳一, 平岡実, and 玄相昊, “駆動輪と受動輪を有する油圧式脚車輪ローバーの 最適接触力制御による4輪及び8輪スロープ走行,” in 第37回日本ロボット学会学術講演会, 2019.
- 井田裕介,石川淳一,平岡実,玄相昊, “油圧式ローバーの最適接触力分配による不整地適応,” in 第24回ロボティクスシンポジア講演論文集, 2019, pp. 112–113.
- 玄相昊,井田裕介,植田晃介,石川淳一,平岡実, “油圧式4脚4輪移動ロボットの全身運動制御,” in 第19回計測自動制御学会システムインテグレーション部門講演会, 2018, pp. 2014–2017.
- 織田健吾, 玄相昊, 油圧式4脚歩行ロボットRL-A1の対称歩行制御による転倒回避と歩行, ロボティクス・メカトロニクス講演会, 2017.
- 織田健吾,塚本泰光,玄相昊,油圧式4脚歩行ロボットRL-A1 の自立化:パワーユニットの搭載,第34回日本ロボット学会学術講演会, 2016.
- 川端健太郎,西拓紀,鳥居裕貴,北浦誠人,兼松宏多,玄相昊,油圧式4脚歩行ロボット RL-A1 の開発,ロボティクス・メカトロニクス講演会, 2014.
- 西拓紀, 鳥居裕貴, 玄相昊, 柔軟な全身接触力制御による4脚歩行ロボットの不整地転倒回避, 第14回システムインテグレーション部門講演会(SI2013), pp.1291-1296, 2013.
- 西拓紀, 富永英介, 鳥居裕貴, 玄相昊, 油圧式4脚走行ロボットの床反力制御と姿勢制御, 第55回自動制御連合講演会, pp.727-730, 2012.
2025/01/29